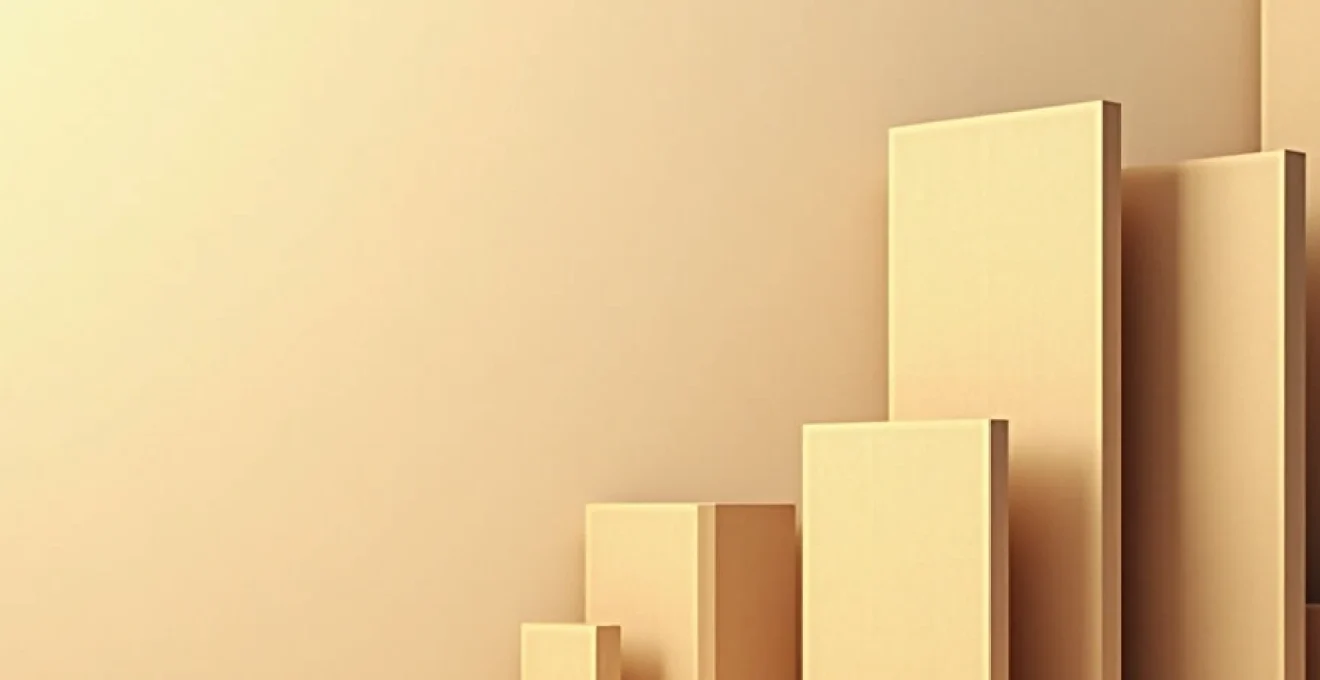
Le panneau de fibres à densité moyenne, communément appelé MDF (Medium Density Fiberboard), est un matériau composite largement utilisé dans l'industrie du meuble et de la construction. Fruit d'une découverte fortuite aux États-Unis en 1966, le MDF s'est rapidement imposé comme une alternative polyvalente et économique au bois massif. Sa structure homogène, sa facilité d'usinage et ses propriétés mécaniques en font un choix privilégié pour de nombreuses applications, allant de la fabrication de meubles à l'agencement intérieur. Plongeons dans l'univers fascinant de ce matériau qui a révolutionné l'industrie du bois.
Composition et structure du panneau MDF
Le MDF se distingue par sa composition unique, qui lui confère des propriétés remarquables. Contrairement au bois massif, le panneau de fibres à densité moyenne est constitué de fibres de bois finement broyées, liées entre elles par une résine synthétique. Cette structure homogène permet d'obtenir un matériau stable et uniforme, sans les défauts naturels que l'on peut trouver dans le bois massif comme les nœuds ou les fissures.
La composition typique d'un panneau MDF comprend environ 82% de fibres de bois, 9% de liant, 8% d'eau et 1% de cire. Les fibres proviennent généralement d'un mélange de bois feuillus et résineux, tels que le chêne, le hêtre, le pin ou l'épicéa. Cette diversité des essences utilisées permet d'optimiser les propriétés du panneau tout en valorisant des ressources forestières variées.
L'un des atouts majeurs du MDF réside dans sa densité, qui oscille généralement entre 600 et 800 kg/m³. Cette densité élevée, comparable à celle de certains bois durs, confère au matériau une excellente stabilité dimensionnelle et une résistance mécanique appréciable. De plus, la finesse des fibres utilisées permet d'obtenir une surface lisse et homogène, idéale pour les finitions de qualité.
La structure interne du MDF, composée de fibres enchevêtrées et liées par la résine, peut être comparée à un tissu dense et compact, offrant une résistance uniforme dans toutes les directions.
Procédé de fabrication industrielle du MDF
La fabrication du MDF est un processus industriel complexe qui requiert une technologie de pointe et un savoir-faire spécifique. Ce procédé, perfectionné au fil des années, permet de transformer des résidus de bois en un matériau performant et polyvalent. Examinons en détail les différentes étapes de cette transformation fascinante.
Préparation des fibres de bois
La première étape consiste à réduire le bois en copeaux. Ces copeaux sont ensuite lavés et triés pour éliminer les impuretés et les particules indésirables. Le déchiquetage du bois est une phase cruciale qui détermine la qualité finale du panneau. Les copeaux sont ensuite soumis à un traitement à la vapeur qui les ramollit et facilite leur transformation en fibres.
Le défibrage proprement dit s'effectue à l'aide de puissants raffineurs qui séparent les fibres de bois les unes des autres. Cette étape est particulièrement délicate car elle influence directement les propriétés mécaniques du panneau final. La finesse et l'homogénéité des fibres obtenues sont essentielles pour garantir la qualité du MDF.
Ajout de liants et additifs
Une fois les fibres obtenues, elles sont mélangées à un liant, généralement une résine urée-formol ou mélamine-formol. Ce liant joue un rôle crucial dans la cohésion du panneau. Des additifs peuvent également être incorporés à ce stade pour améliorer certaines propriétés du MDF, comme sa résistance à l'humidité ou au feu.
L'encollage des fibres est une opération précise qui nécessite un dosage minutieux. La quantité de liant utilisée influence directement les caractéristiques finales du panneau, notamment sa résistance mécanique et sa stabilité dimensionnelle. Trop peu de liant compromettrait la cohésion du panneau, tandis qu'un excès pourrait affecter ses propriétés d'usinage.
Pressage à haute température
Le mélange de fibres encollées est ensuite réparti uniformément pour former un matelas qui sera pressé à haute température. Cette étape de pressage est cruciale car elle détermine l'épaisseur finale du panneau et sa densité. La pression appliquée peut atteindre plusieurs dizaines de bars, tandis que la température s'élève généralement à plus de 200°C.
Le processus de pressage active la polymérisation de la résine, créant des liens solides entre les fibres de bois. C'est durant cette phase que le panneau acquiert sa structure définitive et ses propriétés mécaniques. La durée et les paramètres du pressage sont soigneusement contrôlés pour obtenir les caractéristiques souhaitées.
Finition et découpe des panneaux
Après le pressage, les panneaux sont refroidis et stabilisés. Cette phase de stabilisation est essentielle pour éviter toute déformation ultérieure. Les panneaux sont ensuite découpés aux dimensions standards ou selon les spécifications des clients. La surface des panneaux peut être poncée pour obtenir un fini parfaitement lisse, prêt à recevoir divers revêtements.
La dernière étape consiste à contrôler la qualité des panneaux produits. Des tests rigoureux sont effectués pour vérifier leurs propriétés physiques et mécaniques, garantissant ainsi leur conformité aux normes en vigueur. Les panneaux peuvent alors être emballés et expédiés vers leurs destinations finales.
Propriétés mécaniques et physiques du MDF
Le MDF se distingue par un ensemble de propriétés mécaniques et physiques qui en font un matériau de choix pour de nombreuses applications. Sa structure homogène lui confère des caractéristiques uniques, souvent supérieures à celles d'autres panneaux dérivés du bois. Examinons en détail ces propriétés qui font la renommée du MDF.
Densité et résistance à la flexion
La densité du MDF, généralement comprise entre 600 et 800 kg/m³, lui confère une excellente résistance mécanique. Cette densité élevée se traduit par une bonne résistance à la flexion, un atout majeur pour de nombreuses applications dans l'ameublement. Par exemple, un panneau MDF de 19 mm d'épaisseur peut présenter une résistance à la flexion supérieure à 20 N/mm², ce qui le rend adapté à la fabrication d'étagères ou de plans de travail.
La résistance à la traction perpendiculaire aux faces est une autre propriété remarquable du MDF. Elle témoigne de la cohésion interne du panneau et de sa capacité à résister aux efforts de délaminage. Cette caractéristique est particulièrement appréciée dans la fabrication de meubles assemblés, où les fixations doivent offrir une bonne tenue.
Comportement face à l'humidité
Bien que le MDF standard ne soit pas recommandé pour une utilisation en milieu humide, il existe des versions hydrofuges spécialement traitées pour résister à l'humidité. Ces panneaux MDF hydrofuges présentent un taux de gonflement en épaisseur réduit après immersion dans l'eau, généralement inférieur à 10% pour un panneau de 19 mm d'épaisseur.
Il est important de noter que même les panneaux MDF hydrofuges ne sont pas totalement imperméables. Leur utilisation en extérieur ou dans des zones soumises à une humidité permanente n'est pas recommandée. Cependant, pour des applications intérieures dans des pièces occasionnellement humides, comme les salles de bains, ils offrent une alternative intéressante aux panneaux standards.
Le comportement du MDF face à l'humidité peut être comparé à celui d'une éponge compacte : il absorbe lentement l'humidité mais peut se déformer si l'exposition est prolongée ou intense.
Applications du MDF dans l'industrie du meuble
L'industrie du meuble a rapidement adopté le MDF pour ses nombreux avantages. Sa surface lisse et homogène en fait un support idéal pour les revêtements décoratifs, tandis que sa stabilité dimensionnelle assure la longévité des meubles. Voyons comment ce matériau polyvalent a révolutionné la conception et la fabrication de mobilier.
Dans la fabrication de meubles prêts à monter, le MDF s'est imposé comme un matériau de prédilection. Sa facilité d'usinage permet de créer des pièces aux formes complexes, tandis que sa densité assure une bonne tenue des fixations. Les fabricants apprécient également sa capacité à recevoir divers revêtements, du placage bois au papier mélaminé, offrant ainsi une large gamme de finitions.
Le MDF trouve également sa place dans la fabrication de meubles haut de gamme. Sa surface lisse et sans défaut en fait un support idéal pour les laques et vernis de qualité. Les designers exploitent ses propriétés pour créer des pièces aux lignes épurées et aux finitions impeccables. De plus, la possibilité de cintrer le MDF ouvre de nouvelles perspectives en termes de design, permettant la réalisation de formes courbes et organiques.
Dans l'agencement intérieur, le MDF est largement utilisé pour la réalisation de cloisons, de plafonds suspendus ou de revêtements muraux. Sa stabilité dimensionnelle et sa résistance au feu (dans le cas des panneaux ignifugés) en font un choix judicieux pour ces applications. Les architectes d'intérieur apprécient également sa capacité à être usiné avec précision, permettant la création de motifs et de textures élaborés.
Comparaison MDF vs autres panneaux dérivés du bois
Le marché des panneaux dérivés du bois offre une variété de solutions, chacune ayant ses propres caractéristiques et domaines d'application. Comparer le MDF à ces alternatives permet de mieux comprendre ses avantages et ses limites spécifiques. Examinons comment le MDF se positionne face à trois autres types de panneaux couramment utilisés.
MDF vs panneau de particules
Le panneau de particules, souvent moins dense que le MDF, présente une structure plus grossière composée de copeaux de bois agglomérés. Bien que généralement moins cher, il offre une résistance mécanique inférieure et une surface moins lisse que le MDF. Le panneau de particules est plus sensible à l'humidité et présente une moins bonne tenue des fixations, en particulier sur les chants.
En revanche, le MDF offre une meilleure stabilité dimensionnelle et une surface plus uniforme, idéale pour les finitions de qualité. Il est préféré pour les applications nécessitant un usinage précis ou des finitions haut de gamme. Cependant, le MDF est généralement plus lourd et plus coûteux que le panneau de particules.
MDF vs contreplaqué
Le contreplaqué, composé de feuilles de bois collées en alternant le sens du fil, offre une excellente résistance mécanique et une bonne stabilité dimensionnelle. Il est souvent préféré pour les applications structurelles et résiste mieux à l'humidité que le MDF standard. Le contreplaqué conserve également l'aspect naturel du bois, ce qui peut être un avantage esthétique dans certains cas.
Le MDF, en revanche, présente une surface plus lisse et homogène, idéale pour les finitions peintes ou laquées. Il offre une meilleure tenue des fixations sur toute sa surface et ses chants. Le MDF est généralement moins cher que le contreplaqué de qualité équivalente et permet un usinage plus précis, notamment pour les formes courbes ou les motifs complexes.
MDF vs OSB (oriented strand board)
L'OSB, constitué de grandes lamelles de bois orientées, offre une bonne résistance mécanique et est souvent utilisé dans la construction pour le contreventement ou le support de toiture. Il présente une meilleure résistance à l'humidité que le MDF standard et est généralement moins cher. Cependant, sa surface rugueuse et son aspect caractéristique limitent son utilisation dans l'ameublement ou la décoration intérieure.
Le MDF, avec sa surface lisse et homogène, est nettement supérieur pour les applications nécessitant une finition soignée. Il offre une meilleure stabilité dimensionnelle et une plus grande précision d'usinage que l'OSB. Dans l'industrie du meuble et l'agencement intérieur, le MDF est donc largement préféré à l'OSB.
Caractéristique | MDF | Panneau de particules | Contreplaqué | OSB |
---|---|---|---|---|
Densité | Élevée | Moyenne | Moyenne à élevée | Moyenne |
Surface | Très lisse | Légèrement rugueuse | Lisse (selon le placage) | Rugueuse |
Résistance à l'humidité | Faible (sauf version hydrofuge) | Faible | Bonne | Moyenne à bonne |
Usinabilité | Excellente | Bonne | Bonne | Moyenne |
Coût relatif | Moyen | Faible <!-- |
Enjeux environnementaux et certifications du MDF
Bien que le MDF offre de nombreux avantages techniques et économiques, son utilisation soulève des questions environnementales importantes. L'industrie du MDF est aujourd'hui confrontée à plusieurs défis, notamment en termes d'émissions de formaldéhyde, de recyclage des déchets et de gestion durable des ressources forestières. Examinons ces enjeux et les solutions mises en œuvre pour y répondre.
Émissions de formaldéhyde
L'un des principaux problèmes liés au MDF concerne les émissions de formaldéhyde, une substance classée comme cancérogène par l'Organisation Mondiale de la Santé. Le formaldéhyde est présent dans les résines utilisées comme liant dans la fabrication du MDF. Bien que les niveaux d'émission aient considérablement diminué ces dernières années, cette question reste un sujet de préoccupation pour la santé des consommateurs et des travailleurs de l'industrie.
Pour répondre à ces préoccupations, des normes strictes ont été mises en place dans de nombreux pays. Par exemple, en Europe, la norme E1 limite les émissions de formaldéhyde à 0,1 ppm. Des fabricants proposent désormais des panneaux MDF à très faibles émissions, voire sans formaldéhyde ajouté, utilisant des résines alternatives à base de soja ou de tanins. Ces innovations permettent de réduire significativement l'impact sanitaire du MDF, tout en préservant ses propriétés mécaniques.
Recyclage et valorisation des déchets MDF
Le recyclage du MDF pose des défis techniques importants en raison de sa structure composite. Contrairement au bois massif ou au métal, le MDF ne peut pas être facilement recyclé en fin de vie. La plupart des déchets de MDF finissent actuellement en décharge ou sont incinérés, ce qui soulève des questions environnementales.
Cependant, des solutions innovantes émergent pour valoriser ces déchets. Certaines entreprises développent des technologies permettant de séparer les fibres de bois de la résine, ouvrant la voie à un recyclage plus efficace. D'autres pistes explorées incluent l'utilisation des déchets de MDF comme source d'énergie dans les processus industriels ou leur transformation en paillis pour le jardinage. Ces initiatives, bien qu'encore limitées, montrent que des alternatives à l'enfouissement sont possibles.
Labels PEFC et FSC pour le MDF
Face aux préoccupations concernant la gestion durable des forêts, l'industrie du MDF s'est engagée dans des démarches de certification. Les labels PEFC (Programme for the Endorsement of Forest Certification) et FSC (Forest Stewardship Council) garantissent que le bois utilisé dans la fabrication du MDF provient de forêts gérées de manière responsable.
Ces certifications assurent le respect de critères environnementaux, sociaux et économiques tout au long de la chaîne d'approvisionnement. Elles permettent aux consommateurs de choisir des produits MDF issus de pratiques forestières durables, contribuant ainsi à la préservation des écosystèmes forestiers. De plus en plus de fabricants de MDF s'engagent dans ces démarches de certification, répondant à une demande croissante pour des produits plus respectueux de l'environnement.
L'avenir du MDF réside dans sa capacité à conjuguer performance technique, viabilité économique et responsabilité environnementale. Les innovations en matière de formulations sans formaldéhyde et de recyclage ouvrent la voie à un MDF plus durable.
En conclusion, le panneau de fibres à densité moyenne (MDF) a révolutionné l'industrie du bois et de l'ameublement grâce à ses propriétés uniques et sa polyvalence. Malgré les défis environnementaux qu'il soulève, les efforts continus de l'industrie pour améliorer sa durabilité laissent entrevoir un avenir prometteur pour ce matériau. L'évolution constante des technologies de production et de recyclage, combinée à une prise de conscience accrue des enjeux écologiques, permettra sans doute au MDF de conserver sa place de choix dans nos intérieurs, tout en répondant aux exigences d'un monde plus soucieux de l'environnement.