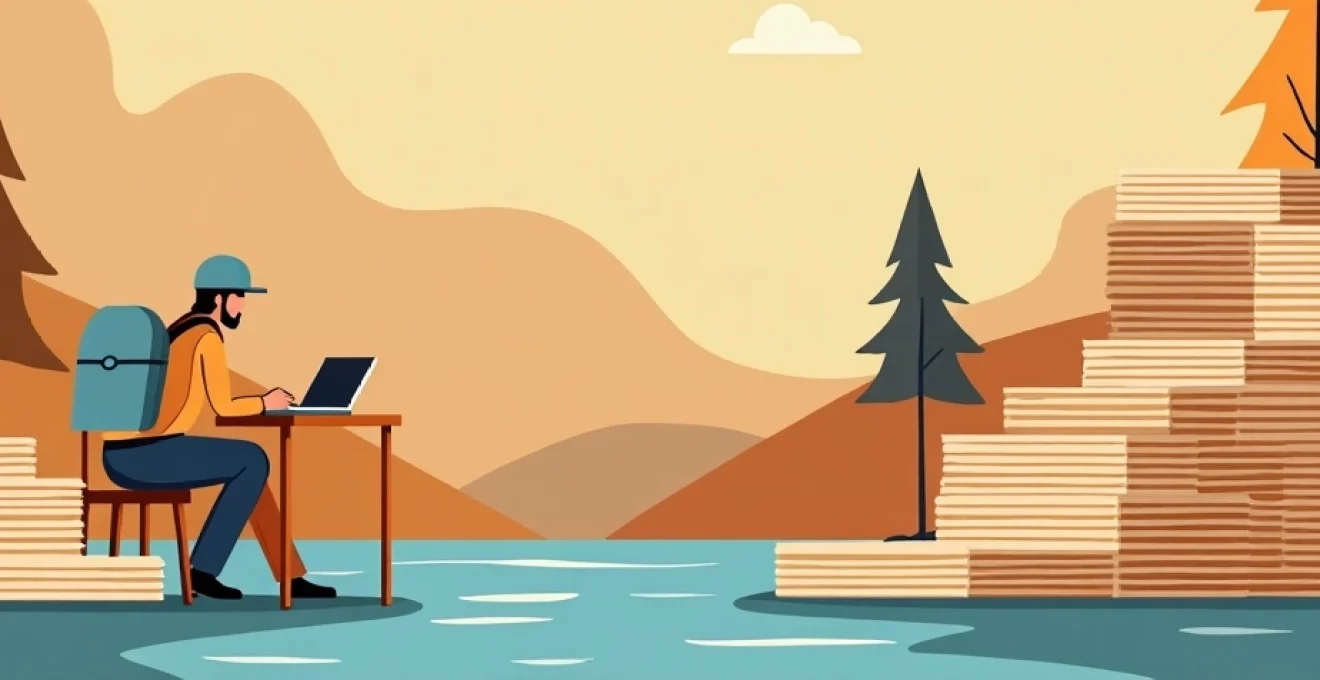
Le contreplaqué est un matériau incontournable dans l'industrie du bois et de la construction. Ce panneau composite, constitué de plusieurs couches de bois collées perpendiculairement les unes aux autres, allie résistance mécanique, stabilité dimensionnelle et polyvalence. Son utilisation s'étend de la construction navale à l'ameublement, en passant par le bâtiment et le design intérieur. Découvrons les coulisses de cette industrie dynamique, ses procédés de fabrication, les essences privilégiées et les innovations qui façonnent son avenir.
Procédés de fabrication du contreplaqué moderne
La fabrication du contreplaqué moderne repose sur un processus bien établi, fruit de décennies d'innovations et d'optimisations. Tout commence par la sélection minutieuse des grumes, qui sont ensuite écorcées et découpées en billons. Ces billons sont ensuite déroulés ou tranchés pour obtenir de fines feuilles de placage.
L'étape cruciale du déroulage consiste à faire tourner le billon contre une lame fixe, produisant ainsi un ruban continu de placage. Cette technique permet d'obtenir des feuilles de grande dimension, optimisant ainsi l'utilisation de la matière première. Le tranchage, quant à lui, est réservé aux bois précieux et produit des placages aux motifs plus esthétiques.
Une fois les placages obtenus, ils sont séchés dans des fours spéciaux pour atteindre un taux d'humidité optimal, généralement entre 6 et 12%. Cette étape est essentielle pour garantir la stabilité future du panneau et optimiser l'adhésion de la colle.
L'encollage des placages est réalisé à l'aide de colles synthétiques, principalement des résines phénoliques pour les panneaux à usage extérieur et des résines urée-formol pour les applications intérieures. Ces adhésifs modernes offrent une résistance à l'humidité et une durabilité nettement supérieures aux colles naturelles utilisées par le passé.
Le pressage des placages encollés s'effectue dans des presses hydrauliques à chaud. La chaleur accélère la polymérisation de la colle, tandis que la pression assure un contact optimal entre les différentes couches. Cette étape est cruciale pour obtenir un panneau homogène et résistant.
Après le pressage, les panneaux sont stabilisés, puis poncés pour obtenir une surface lisse et une épaisseur uniforme. Enfin, ils sont découpés aux dimensions standards ou sur mesure selon les besoins des clients.
L'industrie du contreplaqué ne cesse d'innover pour améliorer ses procédés. L'automatisation et la robotisation des lignes de production permettent d'accroître la productivité tout en maintenant une qualité constante. Des systèmes de vision par ordinateur sont désormais utilisés pour détecter les défauts dans les placages, optimisant ainsi la sélection et l'assemblage des feuilles.
L'utilisation de colles à faible émission de formaldéhyde, voire sans formaldéhyde, est une tendance forte du secteur, répondant aux préoccupations environnementales et sanitaires croissantes. Ces innovations permettent de produire des panneaux plus respectueux de l'environnement et adaptés aux normes les plus strictes en matière de qualité de l'air intérieur.
Essences de bois privilégiées dans l'industrie du contreplaqué
Le choix des essences de bois utilisées dans la fabrication du contreplaqué est déterminant pour les propriétés finales du panneau. Chaque essence apporte ses caractéristiques uniques, influençant la résistance mécanique, la durabilité, l'aspect esthétique et le coût du produit final. Examinons les essences les plus prisées dans l'industrie du contreplaqué et leurs spécificités.
Bouleau de finlande : caractéristiques et avantages
Le bouleau de Finlande est réputé pour sa qualité exceptionnelle dans la fabrication de contreplaqué. Sa structure fine et homogène offre une excellente résistance mécanique et une stabilité dimensionnelle remarquable. Les panneaux en bouleau finlandais se caractérisent par leur surface lisse et leur aspect clair, très apprécié dans l'ameublement haut de gamme et le design intérieur.
L'industrie finlandaise du contreplaqué a développé un savoir-faire unique dans la valorisation de cette essence. La gestion durable des forêts de bouleaux en Finlande garantit un approvisionnement constant et responsable. Les contreplaqués en bouleau finlandais sont particulièrement prisés pour leurs propriétés mécaniques élevées, leur résistance à l'usure et leur capacité à supporter des charges importantes.
Okoumé gabonais : propriétés et applications
L'okoumé, essence tropicale originaire d'Afrique centrale, est largement utilisé dans la fabrication de contreplaqué pour ses propriétés uniques. Son bois léger, de couleur rose saumon, offre un excellent rapport résistance/poids. Les panneaux en okoumé sont particulièrement appréciés dans la construction navale et l'industrie du transport pour leur résistance à l'humidité et leur facilité de mise en œuvre.
La France est le premier producteur mondial de contreplaqué d'okoumé, s'appuyant sur une filière d'approvisionnement historique avec le Gabon. L'utilisation de l'okoumé soulève cependant des questions environnementales, nécessitant une gestion responsable des forêts tropicales pour assurer la pérennité de la ressource.
Pin radiata : polyvalence et rendement
Le pin radiata, également connu sous le nom de pin de Monterey, est une essence à croissance rapide largement cultivée dans l'hémisphère sud, notamment en Nouvelle-Zélande, au Chili et en Australie. Son bois clair et tendre se prête bien à la fabrication de contreplaqué pour des applications variées, du bâtiment à l'emballage.
La polyvalence du pin radiata et son excellent rendement en font une essence prisée par l'industrie. Les panneaux en pin radiata offrent un bon compromis entre coût, performance et impact environnemental, grâce à la gestion durable des plantations.
Eucalyptus : résistance et durabilité
L'eucalyptus, essence originaire d'Australie mais largement cultivée dans de nombreuses régions tropicales et subtropicales, gagne en importance dans l'industrie du contreplaqué. Son bois dense et résistant permet de produire des panneaux de haute qualité, particulièrement adaptés aux applications exigeantes en termes de résistance mécanique et de durabilité.
Les plantations d'eucalyptus à croissance rapide offrent une alternative intéressante aux bois tropicaux traditionnels, réduisant la pression sur les forêts naturelles. L'industrie du contreplaqué en eucalyptus se développe notamment au Brésil, en Uruguay et en Espagne, proposant des produits compétitifs sur le marché international.
Normes et certifications dans la production de contreplaqué
L'industrie du contreplaqué est encadrée par un ensemble de normes et de certifications qui garantissent la qualité, la sécurité et la durabilité des produits. Ces standards jouent un rôle crucial dans la régulation du marché et la confiance des utilisateurs. Examinons les principales normes et certifications qui régissent la production de contreplaqué.
Norme européenne EN 636 : classification et exigences
La norme EN 636 est la référence en Europe pour la classification et les exigences des panneaux de contreplaqué. Elle définit trois classes d'utilisation en fonction des conditions d'humidité auxquelles le panneau sera exposé :
- EN 636-1 pour un usage en milieu sec
- EN 636-2 pour un usage en milieu humide
- EN 636-3 pour un usage en milieu extérieur
Cette norme spécifie également les exigences en termes de propriétés mécaniques, de tolérance dimensionnelle et de qualité de collage. Elle est essentielle pour garantir la performance et la durabilité des panneaux de contreplaqué dans diverses applications.
Certification FSC (forest stewardship council) : traçabilité et gestion durable
La certification FSC est mondialement reconnue comme un gage de gestion forestière responsable et de traçabilité des produits bois. Pour l'industrie du contreplaqué, la certification FSC garantit que le bois utilisé provient de forêts gérées de manière durable, respectant des critères environnementaux, sociaux et économiques stricts.
La chaîne de contrôle FSC assure la traçabilité du bois tout au long du processus de transformation, de la forêt au produit final. Cette certification est particulièrement importante pour les essences tropicales comme l'okoumé, permettant aux consommateurs de faire des choix éclairés en faveur de produits respectueux de l'environnement.
Label PEFC : garantie d'approvisionnement responsable
Le label PEFC (Programme for the Endorsement of Forest Certification) est une autre certification majeure dans l'industrie du bois. Il promeut la gestion durable des forêts à travers un système de certification indépendant. Pour l'industrie du contreplaqué, le label PEFC offre une garantie d'approvisionnement en bois issu de forêts gérées durablement.
Le PEFC est particulièrement répandu en Europe et gagne en importance dans d'autres régions du monde. Il permet aux fabricants de contreplaqué de démontrer leur engagement envers la durabilité et de répondre aux exigences croissantes des marchés en matière de responsabilité environnementale.
Norme américaine PS 1-09 : spécifications pour le contreplaqué structural
Aux États-Unis, la norme PS 1-09 établit les spécifications pour le contreplaqué structural. Cette norme, publiée par le National Institute of Standards and Technology, définit les exigences en matière de performance, de qualité et de marquage pour les panneaux de contreplaqué utilisés dans la construction.
La norme PS 1-09 couvre divers aspects, incluant les types de colles autorisés, les essences de bois acceptables, les grades de placage et les critères de performance structurelle. Elle est fondamentale pour assurer la sécurité et la fiabilité des constructions utilisant du contreplaqué structural aux États-Unis.
Innovations technologiques dans la fabrication du contreplaqué
L'industrie du contreplaqué connaît une véritable révolution technologique, avec l'introduction de nouvelles techniques et d'équipements de pointe visant à améliorer la qualité des produits, l'efficacité de production et la durabilité environnementale. Ces innovations transforment chaque étape du processus de fabrication, de la préparation des placages à la finition des panneaux.
L'une des avancées majeures concerne l'optimisation du déroulage des grumes. Des systèmes de vision par ordinateur couplés à des algorithmes d'intelligence artificielle permettent désormais d'analyser en temps réel la qualité du bois et d'ajuster automatiquement les paramètres de coupe. Cette technologie, appelée smart peeling
, maximise le rendement matière tout en améliorant la qualité des placages obtenus.
Dans le domaine du séchage, de nouveaux fours à micro-ondes offrent un séchage plus rapide et plus uniforme des placages, réduisant la consommation d'énergie et minimisant les déformations. Cette technologie permet également un meilleur contrôle du taux d'humidité final, crucial pour la qualité du collage.
L'encollage bénéficie également d'innovations significatives. Des systèmes d'application de colle par rideau ( curtain coater
) assurent une répartition plus homogène de l'adhésif, réduisant la quantité nécessaire tout en améliorant la qualité du collage. De plus, le développement de colles bio-sourcées, à base de lignine ou de protéines végétales, ouvre la voie à des panneaux plus écologiques.
Le pressage à haute fréquence est une autre innovation marquante. Cette technique permet un durcissement plus rapide et plus uniforme de la colle, réduisant les temps de cycle et améliorant la qualité des panneaux. Elle offre également la possibilité de produire des panneaux de grandes dimensions avec une excellente planéité.
L'industrie du contreplaqué entre dans l'ère de l'Industrie 4.0, avec l'intégration croissante de l'Internet des Objets (IoT) et de l'analyse de données massives pour optimiser les processus de production.
Ces technologies permettent une surveillance en temps réel de la production, une maintenance prédictive des équipements et une traçabilité accrue des produits. L'automatisation et la robotisation des lignes de production se généralisent, améliorant la productivité et la sécurité des travailleurs.
Marchés et applications du contreplaqué dans la construction
Le contreplaqué occupe une place prépondérante dans l'industrie de la construction, grâce à sa polyvalence, sa résistance et sa facilité de mise en œuvre. Les marchés du contreplaqué sont vastes et diversifiés, allant de la construction résidentielle à l'industrie navale, en passant par les travaux publics et l'aménagement intérieur.
Contreplaqué marine : utilisation dans la construction navale
Le contreplaqué marine est un produit phare de l'industrie, spécifiquement conçu pour résister aux conditions les plus exigeantes en termes d'humidité et de salinité. Fabriqué à partir d'essences sélectionnées pour leur durabilité, comme l'okoumé ou le meranti, et assemblé avec des colles phénoliques résistantes à l'eau, ce type de contreplaqué est largement utilisé dans la construction et la réparation de bateaux.
Au-delà de la construction navale traditionnelle, le contreplaqué
marine trouve également des applications dans l'aménagement intérieur des yachts de luxe et des paquebots, où ses propriétés de résistance à l'humidité et son esthétique sont particulièrement appréciées.
Coffrage béton : rôle du contreplaqué dans le BTP
Dans le secteur du bâtiment et des travaux publics, le contreplaqué joue un rôle crucial en tant que matériau de coffrage pour le béton. Les panneaux de contreplaqué, généralement revêtus d'un film phénolique, offrent une surface lisse et résistante pour la coulée du béton, permettant d'obtenir des finitions de haute qualité.
L'utilisation du contreplaqué pour le coffrage présente plusieurs avantages : légèreté, facilité de mise en œuvre, et possibilité de réutilisation. Les panneaux spécialement conçus pour cette application offrent une excellente résistance à l'humidité et aux alcalis du béton, assurant une durée de vie prolongée et une qualité constante des surfaces bétonnées.
L'innovation dans ce domaine se concentre sur le développement de revêtements encore plus performants et sur l'optimisation de la conception des panneaux pour faciliter le décoffrage et réduire l'usure. Certains fabricants proposent désormais des panneaux de coffrage intégrant des capteurs pour suivre en temps réel le processus de durcissement du béton, ouvrant la voie à une gestion plus précise des chantiers.
Contreplaqué décoratif : esthétique et design intérieur
Le contreplaqué ne se cantonne pas aux applications purement fonctionnelles. L'industrie a développé une gamme étendue de panneaux décoratifs qui allient les propriétés techniques du contreplaqué à des finitions esthétiques variées. Ces panneaux trouvent leur place dans l'aménagement intérieur, le mobilier design et l'architecture d'intérieur.
Les contreplaqués décoratifs peuvent être revêtus de placages de bois nobles, offrant l'aspect du bois massif avec les avantages du contreplaqué en termes de stabilité dimensionnelle et de coût. D'autres options incluent des finitions laquées, des impressions numériques ou des textures en relief, ouvrant un vaste champ de possibilités créatives pour les designers et architectes.
Une tendance émergente est l'utilisation de contreplaqués apparents dans le design intérieur, mettant en valeur la structure lamellaire du matériau. Cette approche s'inscrit dans une esthétique minimaliste et authentique, particulièrement appréciée dans les espaces commerciaux et les lofts urbains.
Panneaux structurels : applications dans l'ossature bois
Dans la construction à ossature bois, le contreplaqué joue un rôle structurel majeur. Les panneaux de contreplaqué structurel sont utilisés comme revêtement des murs, des planchers et des toitures, assurant à la fois le contreventement de la structure et une base solide pour les finitions.
Ces panneaux offrent plusieurs avantages par rapport à d'autres matériaux : ils sont légers, faciles à mettre en œuvre, et offrent une excellente résistance mécanique pour leur poids. De plus, leur capacité à agir comme diaphragme structurel permet de répartir les charges latérales (vent, séismes) sur l'ensemble de la structure, améliorant ainsi la résistance globale du bâtiment.
L'industrie travaille constamment à l'amélioration des performances de ces panneaux structurels, notamment en termes de résistance au feu et d'isolation acoustique. Des innovations récentes incluent l'intégration de matériaux isolants directement dans les panneaux, créant ainsi des éléments composites qui simplifient la construction tout en améliorant les performances énergétiques des bâtiments.
Enjeux environnementaux et durabilité de l'industrie du contreplaqué
L'industrie du contreplaqué est confrontée à des défis environnementaux majeurs, notamment en ce qui concerne la gestion durable des ressources forestières et la réduction de son empreinte carbone. Face à ces enjeux, le secteur s'engage dans une démarche de durabilité qui transforme ses pratiques à tous les niveaux.
La question de l'approvisionnement en bois est au cœur des préoccupations. L'industrie s'oriente de plus en plus vers l'utilisation de bois issus de forêts gérées durablement, certifiées FSC ou PEFC. Cette approche vise à garantir le renouvellement des ressources forestières et à préserver la biodiversité. Certains fabricants vont plus loin en développant des partenariats avec des communautés locales pour promouvoir une sylviculture responsable et équitable.
L'optimisation des processus de production est un autre axe majeur de la démarche environnementale. Les usines modernes investissent dans des équipements plus efficients énergétiquement et dans des systèmes de récupération de chaleur. La gestion des déchets est également améliorée, avec un accent mis sur le recyclage et la valorisation des chutes de bois, qui peuvent être utilisées comme biomasse pour la production d'énergie.
L'innovation joue un rôle clé dans la réduction de l'impact environnemental du contreplaqué, avec le développement de colles biosourcées et de traitements plus écologiques.
Ces avancées permettent de réduire les émissions de composés organiques volatils (COV) et d'améliorer la qualité de l'air intérieur des bâtiments utilisant du contreplaqué. Certains fabricants explorent même la possibilité de produire du contreplaqué à partir de matériaux recyclés ou de fibres agricoles, ouvrant la voie à une économie plus circulaire.
La durabilité de l'industrie du contreplaqué passe également par une réflexion sur le cycle de vie complet des produits. Des efforts sont menés pour améliorer la recyclabilité des panneaux en fin de vie, notamment en développant des techniques de séparation des différentes couches et de récupération des colles. Certains fabricants proposent déjà des programmes de reprise et de recyclage de leurs produits, contribuant ainsi à réduire l'impact environnemental global du secteur.
Enfin, l'industrie du contreplaqué s'engage dans une démarche de transparence et de responsabilité sociale. De plus en plus d'entreprises publient des rapports de développement durable détaillant leurs objectifs et leurs progrès en matière environnementale et sociale. Cette approche répond aux attentes croissantes des consommateurs et des régulateurs pour une industrie plus responsable et transparente.
L'avenir de l'industrie du contreplaqué repose sur sa capacité à concilier performance technique, innovation et durabilité environnementale. Les défis sont nombreux, mais les initiatives prises par le secteur montrent une réelle volonté de transformation vers un modèle plus durable, capable de répondre aux enjeux du 21e siècle.