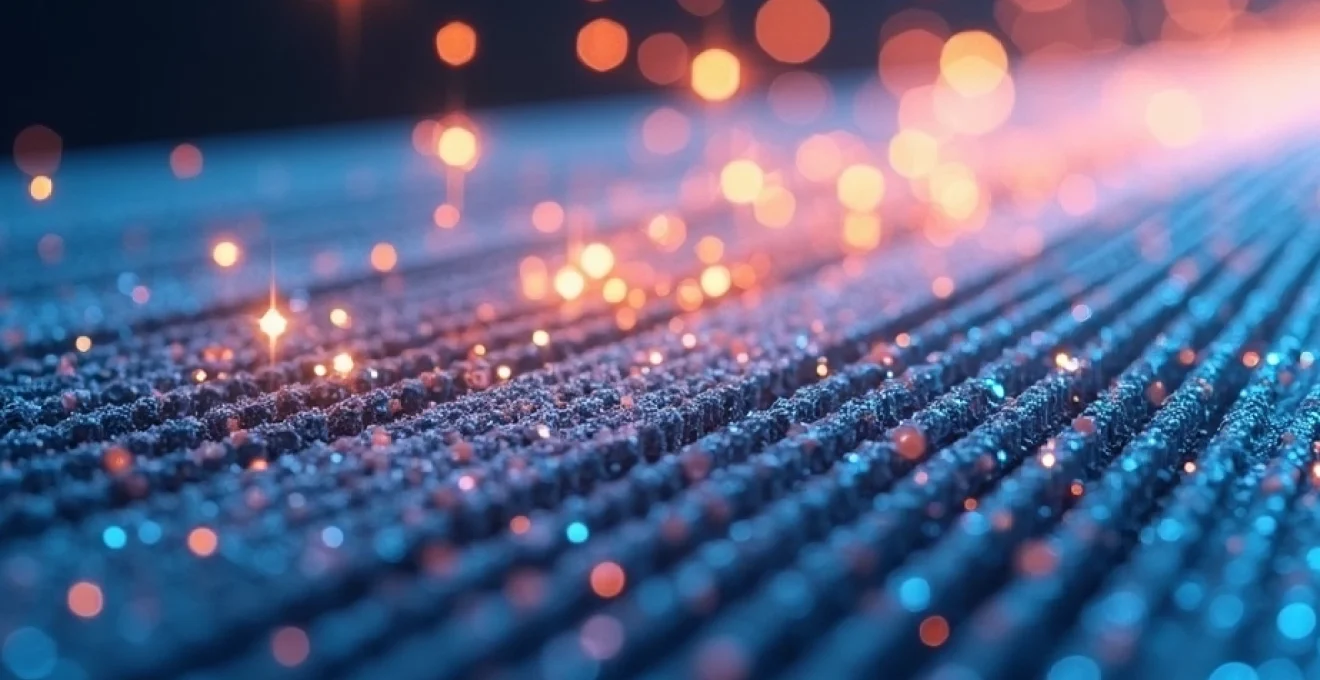
Les matériaux composites révolutionnent de nombreux secteurs industriels grâce à leur légèreté et leur résistance exceptionnelle. Cependant, l'optimisation de leurs propriétés mécaniques reste un défi constant pour les ingénieurs et les chercheurs. En combinant judicieusement différents matériaux et en appliquant des techniques de fabrication avancées, il est possible d'obtenir des composites aux performances remarquables. Découvrez comment repousser les limites de ces matériaux innovants et créer des composites sur mesure pour répondre aux exigences les plus strictes de l'industrie moderne.
Composition et structure des matériaux composites
Les matériaux composites sont constitués de deux composants principaux : la matrice et le renfort. La matrice, généralement un polymère, assure la cohésion et la protection du matériau, tandis que le renfort, souvent sous forme de fibres, apporte la résistance mécanique. La synergie entre ces deux éléments est essentielle pour obtenir des propriétés supérieures à celles des matériaux individuels.
La nature et la proportion de chaque composant influencent directement les caractéristiques finales du composite. Par exemple, une matrice époxy renforcée de fibres de carbone offre une excellente rigidité et résistance, idéale pour les applications aérospatiales. En revanche, un composite à base de fibres de verre dans une matrice polyester sera plus économique et adapté à la construction navale.
L'interface entre la matrice et le renfort joue également un rôle crucial. Une bonne adhésion assure un transfert de charge efficace et prévient la formation de microfissures. Des traitements de surface spécifiques peuvent être appliqués aux fibres pour améliorer cette interface et optimiser les performances mécaniques du composite.
L'art de concevoir un matériau composite performant réside dans la compréhension approfondie des interactions entre ses composants et leur optimisation minutieuse.
Techniques de renforcement des fibres
Les fibres constituent l'épine dorsale des matériaux composites, assurant leur résistance et leur rigidité. Plusieurs techniques permettent d'améliorer leurs propriétés et, par conséquent, celles du composite dans son ensemble.
Optimisation de l'orientation des fibres
L'orientation des fibres dans un composite a un impact majeur sur ses propriétés mécaniques. En alignant les fibres dans la direction des contraintes principales, on maximise la résistance du matériau. Cette technique est particulièrement efficace pour les pièces soumises à des charges unidirectionnelles, comme les mâts d'éoliennes ou les cadres de vélos de compétition.
Pour des applications nécessitant une résistance multidirectionnelle, on peut opter pour des stratifiés avec des couches de fibres orientées différemment. Cette configuration permet d'obtenir des propriétés quasi-isotropes, adaptées à des sollicitations complexes. Les ingénieurs utilisent souvent des logiciels de simulation pour optimiser l'empilement des couches en fonction des contraintes spécifiques de chaque application.
Traitement de surface des fibres de carbone
Les fibres de carbone sont réputées pour leur excellente résistance spécifique, mais leur surface lisse peut limiter l'adhésion avec la matrice. Des traitements de surface spécifiques permettent d'améliorer cette interface cruciale. L'oxydation contrôlée de la surface des fibres crée des groupes fonctionnels qui favorisent les liaisons chimiques avec la matrice polymère.
Un autre traitement prometteur consiste à déposer une fine couche de nanotubes de carbone sur les fibres. Cette nano-fonctionnalisation augmente considérablement la surface de contact et crée une zone de transition graduelle entre la fibre et la matrice, améliorant ainsi le transfert de charge et la résistance à la rupture du composite.
Incorporation de nanotubes de carbone
Les nanotubes de carbone (NTC) représentent une avancée majeure dans le domaine des renforts pour composites. Leur structure unidimensionnelle et leurs propriétés mécaniques exceptionnelles en font des candidats idéaux pour améliorer les performances des matériaux composites traditionnels.
L'incorporation de NTC dans la matrice ou à l'interface fibre-matrice peut augmenter significativement la ténacité et la résistance à la fatigue du composite. Cependant, la dispersion homogène des NTC reste un défi technique. Des techniques comme la sonication ou la fonctionnalisation chimique des nanotubes sont utilisées pour améliorer leur compatibilité avec la matrice et éviter les agglomérations qui pourraient fragiliser le matériau.
Utilisation de fibres hybrides kevlar-carbone
La combinaison de différents types de fibres dans un même composite permet de tirer parti des avantages de chacune. Les fibres hybrides kevlar-carbone sont un excellent exemple de cette approche. Le kevlar apporte sa résistance exceptionnelle à l'impact et sa ténacité, tandis que les fibres de carbone contribuent à la rigidité et à la résistance en traction.
Cette synergie permet de créer des composites plus performants et plus polyvalents. Par exemple, dans l'industrie aérospatiale, ces composites hybrides sont utilisés pour fabriquer des panneaux qui doivent résister à la fois aux charges en vol et aux impacts potentiels de débris.
L'hybridation des fibres ouvre la voie à des matériaux composites sur mesure, capables de répondre à des cahiers des charges toujours plus exigeants.
Modification de la matrice polymère
La matrice joue un rôle crucial dans les performances globales du composite. Sa modification peut significativement améliorer les propriétés mécaniques, thermiques et chimiques du matériau final.
Ajout de nanoparticules d'argile
L'incorporation de nanoparticules d'argile dans la matrice polymère est une technique prometteuse pour améliorer les propriétés des composites. Ces nanoparticules, lorsqu'elles sont bien dispersées, créent une structure en labyrinthe qui renforce la matrice et améliore sa résistance thermique et chimique.
La clé réside dans l'exfoliation des plaquettes d'argile pour maximiser leur surface de contact avec le polymère. Des techniques comme l'intercalation in situ ou la polymérisation intercalaire permettent d'obtenir une dispersion optimale. Les nanocomposites ainsi obtenus présentent souvent une amélioration significative de leur module d'Young et de leur résistance à la traction, tout en conservant une bonne ductilité.
Réticulation contrôlée des résines époxy
Les résines époxy sont largement utilisées comme matrices dans les composites hautes performances. Le contrôle précis du processus de réticulation permet d'optimiser les propriétés mécaniques du matériau final. En ajustant la nature et la proportion des agents de réticulation, ainsi que les conditions de cure (température, pression), on peut moduler la densité du réseau tridimensionnel formé.
Une réticulation plus dense augmente généralement la rigidité et la résistance thermique du composite, mais peut le rendre plus fragile. À l'inverse, une réticulation moins dense peut améliorer la ténacité au détriment de certaines propriétés mécaniques. L'utilisation d'agents de réticulation multifontionnels ou de mélanges d'agents permet d'atteindre un équilibre optimal entre ces différentes propriétés.
Incorporation d'élastomères thermoplastiques
L'ajout d'élastomères thermoplastiques dans la matrice thermodurcissable est une stratégie efficace pour améliorer la ténacité des composites sans compromettre significativement leur rigidité. Ces élastomères forment une phase dispersée qui agit comme des îlots de déformation plastique, absorbant l'énergie lors de la propagation des fissures.
La compatibilisation entre l'élastomère et la matrice est essentielle pour obtenir une dispersion fine et homogène. Des techniques comme la modification chimique des élastomères ou l'utilisation de compatibilisants permettent d'optimiser cette interface. Les composites ainsi modifiés présentent une résistance accrue à la propagation des fissures et une meilleure tolérance aux dommages, particulièrement appréciées dans les applications aérospatiales et automobiles.
Procédés de fabrication avancés
Les techniques de fabrication jouent un rôle crucial dans la qualité et les performances des matériaux composites. Des procédés avancés permettent d'obtenir des pièces avec moins de défauts, une meilleure consolidation et des propriétés mécaniques optimisées.
Moulage par transfert de résine (RTM)
Le moulage par transfert de résine (RTM) est une technique qui offre un excellent contrôle de la qualité et de la reproductibilité des pièces composites. Dans ce procédé, les fibres sèches sont placées dans un moule fermé, puis la résine est injectée sous pression. Cette méthode permet d'obtenir des pièces avec un taux de fibres élevé et une faible porosité, deux facteurs clés pour de bonnes propriétés mécaniques.
Les avancées récentes en RTM incluent l'utilisation de résines à faible viscosité et de systèmes d'injection à débit variable. Ces innovations permettent une meilleure imprégnation des fibres, même pour des géométries complexes, et réduisent le risque de zones sèches ou mal imprégnées qui pourraient fragiliser la pièce.
Infusion sous vide assistée par film (VARTM)
L'infusion sous vide assistée par film (VARTM) est une variante du RTM qui utilise le vide pour attirer la résine dans le renfort fibreux. Cette technique présente l'avantage de nécessiter des outillages moins coûteux que le RTM traditionnel, tout en offrant une excellente qualité de pièces.
Le VARTM est particulièrement adapté à la fabrication de grandes pièces, comme des coques de bateaux ou des pales d'éoliennes. L'utilisation de films perforés et de tissus drainants optimise la circulation de la résine et assure une imprégnation homogène. De plus, le contrôle précis du vide permet de moduler la pression de consolidation et d'obtenir des taux de fibres élevés, améliorant ainsi les propriétés mécaniques du composite.
Fabrication additive de composites
La fabrication additive, ou impression 3D, ouvre de nouvelles perspectives pour la conception et la production de composites. Cette technologie permet de créer des structures complexes et optimisées, impossibles à réaliser avec les techniques traditionnelles.
Plusieurs approches sont explorées, comme l'impression de fibres continues imprégnées de résine ou la déposition de fibres courtes dans une matrice thermoplastique. Ces techniques permettent un contrôle précis de l'orientation des fibres à l'échelle microscopique, optimisant ainsi les propriétés mécaniques dans des directions spécifiques.
Un avantage majeur de la fabrication additive est la possibilité de créer des structures biomimétiques , inspirées de la nature. Par exemple, des composites imprimés en 3D imitant la structure interne des os ou des coquillages montrent des propriétés mécaniques remarquables, combinant légèreté et résistance.
La fabrication additive de composites représente une véritable révolution, permettant de concevoir et de produire des matériaux aux propriétés mécaniques sur mesure, adaptés à chaque application spécifique.
Caractérisation et tests mécaniques
Pour optimiser les propriétés mécaniques des matériaux composites, il est essentiel de disposer de méthodes de caractérisation précises et fiables. Ces techniques permettent non seulement d'évaluer les performances des matériaux développés, mais aussi de comprendre les mécanismes de défaillance et d'orienter les efforts d'amélioration.
Analyse par éléments finis (FEA)
L'analyse par éléments finis (FEA) est un outil puissant pour prédire le comportement mécanique des composites. Cette méthode numérique permet de simuler la réponse du matériau à différentes sollicitations, en tenant compte de sa structure complexe et anisotrope.
Les modèles FEA avancés intègrent des informations détaillées sur la microstructure du composite, comme l'orientation des fibres et les propriétés de l'interface fibre-matrice. Ces simulations permettent d'optimiser la conception des pièces composites avant même leur fabrication, réduisant ainsi les coûts et les délais de développement.
Essais de traction et de compression
Les essais de traction et de compression sont fondamentaux pour caractériser les propriétés mécaniques des composites. Ces tests fournissent des informations cruciales sur le module d'Young, la résistance à la rupture et l'allongement à la rupture du matériau.
Pour les composites, ces essais doivent être réalisés dans différentes directions pour évaluer l'anisotropie du matériau. Des techniques avancées comme la corrélation d'images numériques (DIC) permettent de mesurer avec précision les champs de déformation locaux, offrant une compréhension plus fine du comportement du matériau sous charge.
Évaluation de la résistance à l'impact
La résistance à l'impact est une propriété critique pour de nombreuses applications des composites, notamment dans l'aérospatiale et l'automobile. Des tests normalisés comme l'essai Charpy ou l'impact à chute de masse sont couramment utilisés pour évaluer cette propriété.
Des techniques plus avancées, comme l'analyse par émission acoustique, permettent de suivre en temps réel l'initiation et la propagation des dommages lors de l'impact. Ces informations sont précieuses pour développer des composites plus résistants aux chocs et mieux comprendre les mécanismes d'absorption d'énergie dans ces matériaux.
Microscopie électronique à balayage (MEB)
La microscopie électronique à balayage (MEB) est un outil indispensable pour l'analyse fine de la microstructure des composites. Cette technique permet d'observer à très
haute résolution la structure interne des composites, révélant des détails cruciaux sur l'interface fibre-matrice, la dispersion des renforts et les mécanismes de rupture.L'utilisation de MEB environnemental permet d'observer les échantillons sans préparation spéciale, réduisant le risque d'artefacts. De plus, couplée à des techniques comme la spectroscopie à dispersion d'énergie (EDS), la MEB fournit des informations précieuses sur la composition chimique locale du composite.
L'analyse des surfaces de rupture par MEB est particulièrement instructive. Elle permet d'identifier les modes de défaillance dominants, comme la rupture des fibres, le délaminage ou la décohésion fibre-matrice. Ces informations sont essentielles pour améliorer la conception des composites et optimiser les interfaces entre les différents composants.
La caractérisation approfondie des matériaux composites, combinant des techniques avancées comme la FEA, les essais mécaniques et la microscopie, est la clé pour développer des matériaux toujours plus performants et adaptés aux exigences spécifiques de chaque application.
En conclusion, l'amélioration des propriétés mécaniques des matériaux composites est un domaine en constante évolution, qui bénéficie des avancées dans la science des matériaux, les procédés de fabrication et les techniques de caractérisation. La combinaison judicieuse de renforts innovants, de matrices optimisées et de méthodes de fabrication avancées permet de créer des composites sur mesure, capables de répondre aux défis les plus exigeants de l'industrie moderne.
L'avenir des matériaux composites s'annonce prometteur, avec des développements passionnants dans des domaines tels que les nanocomposites, les composites auto-réparants et les structures biomimétiques. Ces innovations ouvrent la voie à une nouvelle génération de matériaux plus légers, plus résistants et plus durables, qui joueront un rôle crucial dans la transition vers une économie plus durable et efficiente en ressources.